How Injuries Impact Women In Automobile Supply Chain
Women workers are vulnerable due to gender wage disparity, lack of proper training, and difficulty in accessing legally entitled post-accident support.
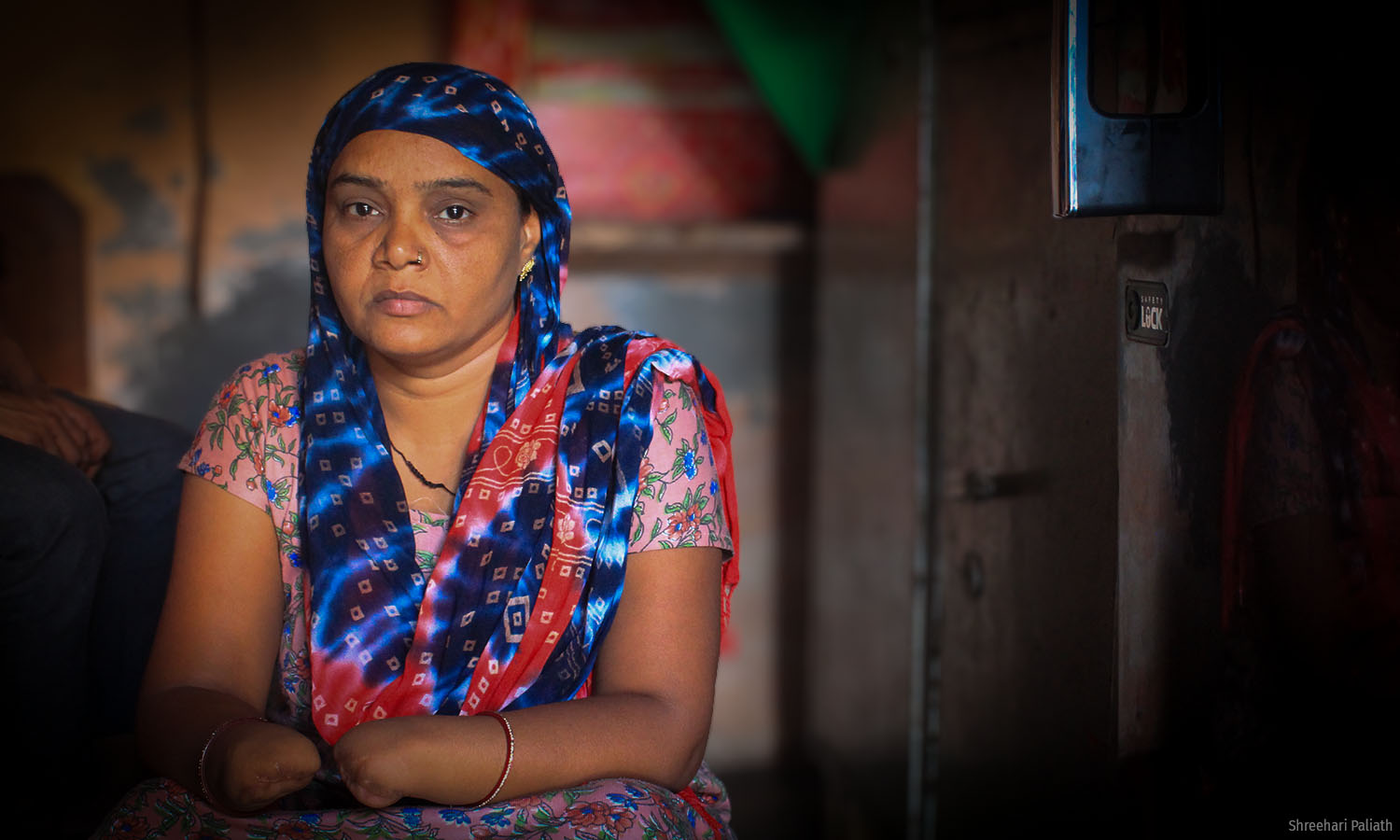
Basanti worked as a power press operator in a Faridabad automobile components factory. In November 2023, her hands were amputated after they were crushed in a power press machine
Warning: Images in this story are graphic in nature and might be disturbing for some viewers.
Faridabad and Bengaluru: Thirty-seven-year-old Basanti, a migrant worker originally from Rajasthan’s Dholpur, has struggled to regain her daily rhythm in the last seven months.
On a Sunday in November 2023, when her supervisor demanded that she come to the automobile component factory in Faridabad where she worked as a power press operator, she was reluctant. If she didn’t comply in order to help meet an urgent order, Basanti was told, she would be sacked from the company she had toiled for 10 hours each day for the last two years.
“When I arrived, I told the supervisor that the machine was unsafe and had been so for around six months. It is usually operated by another person who was on leave that day,” Basanti told IndiaSpend. “The machine had almost crushed my hand thrice that day before the accident. But I was forced to operate it to meet production demand.”
Her hands were amputated after they were crushed in the ill-maintained power press. Now, she depends on an attendant family member, usually her daughter, to be fed, bathed, and dressed. “I just want my hand to be [surgically] replanted so that I can go on with my life,” she said.
Her case is not an aberration in the profitable automobile sector. Since 2016, there have been more than 5,000 auto sector injuries, where workers have lost two fingers, on average, according to ‘Crushed 2023’, a report by civil society organisation Safe in India Foundation (SII). These incidents were recorded in the supply chain of more than 20 automobile brands or original equipment manufacturers (OEMs). Most of these workers whom SII has assisted in accessing Employees' State Insurance Corporation (ESIC) entitlements, like medical support and pension, are in Haryana and Maharashtra.
According to Automotive Component Manufacturers Association of India (ACMA), the apex body representing the automotive component industry, the industry grew 33% annually to $70 billion (Rs 5.6 lakh crore) in 2023, while auto components supply to OEMs grew 40%. Basanti earned a meagre Rs 10,000 (about $120) a month for a job that she was never technically trained to perform.
Data from the Society of Indian Automobile Manufacturers (SIAM), the national body representing all major vehicle and vehicular engine manufacturers, show that the automotive industry provided direct and indirect employment to an estimated 32 million people in 2016. It has the potential to add 65 million jobs by 2026, and to generate $300 billion (Rs 25 lakh crore) in revenue, a contribution of 12% of the country’s gross domestic product.
Despite impressive profits and growth, however, in the lower tiers of the supply chain, workers’ safety overall--and women workers’ vulnerability in particular--is exploited, IndiaSpend found in the course of ground reporting in Faridabad. Women workers, most of whom are poor and migrants, are particularly vulnerable due to gender wage disparity, illiteracy and lack of proper training to operate power presses, lack of job opportunities post accidents, family pressure, and difficulty in accessing legally entitled post-accident support.
Disregard for workers’ safety and lack of training
More than 3.1 million women were employed in India’s registered factories in 2021, based on the latest data available with the Directorate General Factory Advice Service and Labour Institutes (DGFASLI), the technical arm of the labour ministry which deals with matters related to Occupational Safety and Health (OSH) in factories and dock works of major ports. In 2021, more than half a million women worked in Haryana’s factories, the most after Tamil Nadu.
DGFASLI collects OSH statistics from state chief inspectors of factories and directors of industrial safety and health. These data represent only registered factories, although about 90% of workers in India are employed in the informal sector, IndiaSpend reported in January 2023.
A short drive away from Basanti’s one-room rented home, which she shares with her husband--a daily wager--and their three children in Faridabad’s Ballabgarh, 32-year-old Shyamvati, a power press operator, is unable to come to terms with her injuries.
In April 2024, Shyamvati’s life was upturned after her left hand was crushed in the power press of an automotive component supplier of major OEMs. Except her left index finger, which is numb and immobile, all others were amputated and had not healed when IndiaSpend met her in June.
A power press machine is used in the automobile industry for cutting and shaping metal which reduces labour and time to produce material. At least two-thirds of the injuries in Haryana, Maharashtra and Uttarakhand, based on SII’s analysis for 2023, are from power presses and mostly due to bad maintenance. In Haryana, at least half of the injuries since 2016 were due to power presses.
Haryana is one of the major auto sector hubs, and Faridabad and Gururgam have high concentrations of automobile component manufacturing units.
Shyamvati, a migrant from Rajasthan’s Bharatpur, cannot use her left hand as it was crushed in the power press of an automotive component factory. Poorly maintained power press machines account for a majority of injuries in this sector.
Shyamvati had been her family’s primary earner ever since her husband, a daily wager, developed health issues soon after they moved to Faridabad from Rajasthan’s Bharatpur more than a decade ago. She earned Rs 13,200 (about $160) a month, which was more than the salary earned by other women operators.
“Doctors say there isn’t much that they can do,” said Shyamvati, who needs four tablets each day just to manage her pain.
Immediately after her accident, she was paid Rs 2,700 for four days of work in April, and advised by the factory representatives to take Rs 10,000 as settlement/compensation instead of pursuing a legal case which, they said, would be a financial burden for her. “I do not think they will give me a job. When I went to meet them, they did not even offer a glass of water.”
Like Basanti, Shyamvati too faced workplace humiliation if she did not meet production requirements on the faulty and unsafe machine that eventually maimed her arm. “When I was cleaning the machine, I noticed that the power press started working on its own, which I promptly pointed to the supervisor,” she said. “I was told to go home if I did not want to work, and was pressured to ensure production quality on a machine which did not have a proper safety sensor.”
Now without an income and a loan of more than Rs 1 lakh, Shyamvati had to pull out her three young children aged 12, 11 and 9 years, from school. She and the children now live with her sister--120 km away in Uttar Pradesh’s Mathura--because cooking and other household responsibilities have almost become impossible, she said. “My daughter is too young to help out and my husband has to manage on his own here,” said a worried Shyamvati.
Women’s workforce under increasing stresses
Basanti and Shyamvati are both migrants who gained employment through contractors. Most workers in this sector are young migrants in non-permanent roles, and unlikely to be part of a labour union, said SII’s report.
Women’s labour force participation has been a cause for concern in India. The workforce participation rate for women rose during the growth slowdown, but most of the increase was in self-employment, said the State Of Working India (SWI) 2023 report.
On average, Indian women spend over 44 hours a week on unpaid domestic work and caregiving activities, IndiaSpend reported in January 2024. In comparison, men spend just over five hours a week on these activities.
Nisha Srivastava, economist and visiting faculty at the Institute for Human Development, Delhi said that these accidents were not inevitable and can be avoided. It would not cost the automobile sector too much to ensure workers’ safety. “The conditions do not favour any worker, and women are relatively worse off,” she said. “I think it is desperation that leads people to such jobs.”
Between 2017 and 2021, 10 people were injured each day, on average, due to accidents in India's registered factories, and there were nearly 3,800 accidents each year. Over 395 million workers worldwide sustained a non-fatal work injury in 2019, according to 2023 International Labour Organization's data.
Workers generally start as helpers, assisting a power press operator and doing minor jobs like removing scrap and loading work pieces. Basanti and Shyamvati were helpers who learned to operate power presses on the job, without formal training. While Shyamvati has completed high school, Basanti has not attended school. Often, workers are not educationally qualified to be helpers or press shop assistants, which requires them to have completed grade VIII. Most of the women that IndiaSpend spoke with said they had not completed primary school or had not attended school at all.
Accidents are under-reported Between 2017 and 2021, the DGFASLI recorded 18,956 non-fatal injuries in India. The number of non-fatal injuries fell 1.2% from 2020 to 2,803 in 2021. In a February 2024 right-to-information response to a request for the latest data until 2023, DGFASLI said that the information was available on the website, which as on July 1, does not have data after 2021. Further, the data do not have gender-based accident information, and the RTI response said that such data are not available. Data that are available are under-reported. For example, ‘Crushed 2023’ reported that SII assisted 803 injured workers in Haryana in 2021. DGFASLI data however show 24, the least it reported between 2017 and 2021. While data are not available with DGFASLI, SII has reported an increase of 27% and 55% of injured workers supported in 2022 and 2023 respectively, compared to its 2021 data. Further, ESIC data show that in 2021, there were 712,285 employees potentially exposed to employment injuries in Faridabad, which increased 13% to 801,250 the following year. Across Haryana (Faridabad, Gurugram and Karnal), there were 2 million employees potentially exposed to employment injuries; across India, there were 29.2 million. ESIC’s data also show that 678 new cases of workers requiring permanent disability benefits were admitted from Faridabad and Gurugram in 2021. These numbers should ideally reflect on DGFASLI also, but do not. In 2022, there were 696 cases per ESIC data. V.N. Saroja, head of advocacy, worker safety and ESIC initiative at SII, said that the government systems have data, but they are in silos and do not talk to each other. “While workers are getting injured and getting ESI treatment including permanent disability benefit, all accidents, based on the injuries we observe, are clearly not getting recorded by DGFASLI or the labour ministry.” According to the Industrial Safety and Health division state officials, when ESI shares data, it has the name of the contractor through whom workers gained employment, and some they claim are not factory accidents. There are issues of classification and loopholes get exploited, said Saroja. Srivastava feels that data are important for transparency and quick action. She suggests a portal like the rural jobs programme, which provides data on millions of workers routinely. “But there is hardly any data regarding accidents except limited and unreliable data from DGFASLI. It should be easy to set up a portal for this sector that gives real time information on industrial accidents.” DGFASLI data show that 14,332 of about 125,000 injuries recorded in a decade to 2021 were due to machinery--that is, one in nine injuries reported during the time period. But in 2021, there were around 9,000 prosecutions under Section 92 (general penalty for offences) and 96A (penalty for contravention of the provisions relating to hazardous process) of the Factories Act, 1948 that were launched, in addition to 47,984 pending cases. Of the 5,012 convictions, only eight led to imprisonment while Rs 6.5 crore was the reported penalties imposed. |
The ‘Crushed’ report finds that in Haryana, Maharashtra and Uttarakhand, 13-24% of injured workers were helpers. But helpers and operators face a similar incidence of losing fingers, said the report based on data from Gurugram, Faridabad, Pune and Rudrapur. A high proportion of injured helpers suggests that unskilled workers were being asked to do a skilled job, which is illegal, said the report.
IndiaSpend has written to the labour ministry and Haryana’s labour commissioner for comment on the government’s plan to improve worker safety, support for women workers and wage-related problems, tracking accidents in the automobile supply chain, and access to government's social security entitlements for injured workers.
We have sent a similar set of questions to the senior management at SIAM and ACMA for their responses on workers’ safety in the supply chain and the support offered. We will update the story when we receive responses.
Mapping the supply chain and safety policy
“[The] Automobile industry in India has a wide and deep supply chain. The production model seeks low and cheap costs including labour,” said Shyam Sundar, a labour economist and adjunct faculty at Management Development Institute (MDI), Gurgaon. “As we go down the supply chain, most regulations are weak.”
None of the 10 OEMs analysed by SII in its 2023 Safety Niti report on OSH policies for their supply chain had an OSH implementation plan for the deeper supply chain. This had not changed in the previous two years.
In an interview with IndiaSpend in November 2023, Sandeep Sachdeva, co-founder and CEO of SII, had said that OEMs should prioritise the implementation of the minimum required actions to prevent these injuries, like mapping their deeper supply chains at least to Tier 3 suppliers, that is, three levels of suppliers, as also quality audits to Tier 1, Tier 2, and Tier 3 suppliers, and establishing grievance redressal mechanisms that extend to these tiers.
India passed four labour codes to modernise and simplify existing labour regulations by 2021. The rules however have still not been framed by all states. The government planned to conduct a workshop for states to help a nationwide roll out, said a June 2024 Business Standard report. But there are media reports that trade unions want the labour codes scrapped.
The draft rules under Occupations Safety, Health and Working Conditions (OSH and WC) Code 2020 published by the Haryana labour department mentions various requirements to ensure fitness of power press, its safety and operation, and action to be taken if safety problems have been found. The model rules of the Factory Act 1948 published on DGFASLI demand similar requirements to operate power presses.
A circular on power press operating guidelines issued by the Maharashtra government to industries operating power presses during the peak of Covid-19 in May 2020 said that workers working on such machines shall be informed about the hazards of operating it and “trained and instructed in the safe method of work before starting work on any power press machine”.
Based on the experience of workers, these regulations seem to be violated routinely, and safety neglected.
Sundar said that vendors are dispersed across regions and beyond Tier-2 (smaller units manufacturing auto components), due to which OEMs may not know where it has been sourced. “There is no mapping of production, which means there is no question of labour law regulation. The mapping is not linear, that is, it may be sourced from Tier 1 for an OEM and a Tier 2 or 3 for another.”
The number of factory inspectors, vital in the safety system to ensure monitoring of lapses and checking records for injuries, fatalities and procedural issues, is inadequate. In 2021, one in three sanctioned posts of inspectors remained vacant. There was one factory inspector for every 417 working factories, and in Haryana there was one for every 604 working factories.
Further, safety audits do not usually happen in their presence, some of the workers said, impacting transparency. More than half of the injured workers operating power press machines reported that either audits did not happen in their presence, or they were asked to leave during audits, said the ‘Crushed’ report.
This impacts transparency, because there are no grievance redressal mechanisms specifically about the safety and performance of machines like power presses, which cause accidents.
OEMs do not seem to blacklist factories where accidents happen repeatedly because the supply chain is so tightly knit that replacing a component supplier may not be immediately possible, said V.N. Saroja, head of advocacy, worker safety and ESIC initiative at SII.
“The government should use technology and data to identify hot spots where accidents occur and use data to increase probability of inspections in badly run factories rather than give equal weightage to all factories,” she said.
‘We do more work than men’
IndiaSpend spoke to multiple women workers who had injuries due to power press machines. None of them were trained or educationally qualified to operate these machines. They started as helpers assisting operators, earning between Rs 6,000 and Rs 8,000 a month for eight hours of work, and were compelled to become operators with minimal and inadequate training--a situation they accepted because wages were better.
Urban male plant and machine operators and assemblers in India earned Rs 15 per hour more, on average, than urban female workers who earned Rs 43 per hour, according to the Union government’s Women and Men in India 2022 report.
India has one of the widest gender-based wage disparity in the world. According to the Global Gender Gap Index 2024, India is ranked 142 among 146 countries in economic participation and opportunity. It is placed only higher than Pakistan, Iran, Sudan and Bangladesh in terms of economic parity. Overall, India ranks, down two places from 2023.
Gender wage disparity exists across the board, said Srivastava. “The tragedy here is the accidents and its impact. In other sectors this may not be the case,” she said.
In April 2024, it had only been a month since Kavita, 34, had joined her new workplace when her two fingers were crushed in a power press machine. Since she separated from her husband who subjected her to domestic violence, Kavita had been staying in a rented room with her mother for over five years. More than a quarter of her salary is spent on rent and electricity each month. She said that she had received a month’s salary from the contractor and was hoping that they would pay her until she recovers. Although the company has asked her to return to work, it is for a helper’s job which pays less.
“I joined for a monthly salary of Rs 10,500 because I had family compulsions and needed a job,” said Kavita, who has never attended school. “Men get more than women because they say that women waste time. In fact we do more [work] than the men.”
On average, women earn 76% of what men earn in salaried work, which drops to only 40% for the self-employed, said the 2023 SWI report.
Some women workers said that men may have to work on setting dies (a specialised tool to cut metal) in the power press, or lifting heavy parts which are physically laborious. But that was not a valid reason for women to be paid less for the same type of work and production needs, they said.
Seema Sharma, a field executive in SII’s Faridabad centre, said that both male and female workers have similar issues, but the pressure--work and family--is more on women. “Women get less wages despite doing more work. Many women are not able to fight for their rights because they are unable to find other jobs [after accidents] and it affects their family.”
Kavita’s fingers were crushed in a power press within a month of joining an automobile component factory in Faridabad. She is worried she will not find a job due to her injury.
The women workers IndiaSpend spoke to said that they worked more than eight hours a day and more than 48 hours a week, which was above the prescribed limit under the OSH Code 2020. Most said that they were paid by the hour, without overtime pay. Workers are entitled to overtime pay of twice the daily wage rates, according to Factories Act,1948.
Two-thirds of injured workers reported having worked more than 60 hours a week, said the SII’s Crushed 2023 report, and 26% worked more than 48 hours.
“Non-payment of equal wages for equal work is a historical malaise,” said Sundar. The gender-based wage differential exists in the most advanced industries, not just lower tiers of production, and prevails across industries. Even though there is an Equal Remuneration Act, 1976 which requires employers to pay for equal work, it is a legislation that is least discussed but most exploited, he said.
Lack of empathy and accessing post-accident treatment
For workers who have lost limbs, the future feels bleak. They are unable to find work in other factories, they said. Contractors check their hands and feet for injuries before they consider employment, which limits opportunities for all workers, particularly affecting women workers who have to contend with mobility and network to find new jobs.
Immediately after an accident, workers fight an uphill battle to avail their medical entitlements under the ESIC, which helps access healthcare entitlement during sickness, maternity, disablement and death due to employment injury and to provide medical care to insured persons and their families.
Two in three workers in Haryana said that they received their ESIC e-Pehchan (identity) card after the accidents, while more than 75% said so in Maharashtra.
ESIC applies to factories and other establishments like road transport, hotels, restaurants etc where 10 or more persons are employed. Employees drawing wages up to Rs 21,000 a month, are entitled to social security cover under the ESI Act.
Forty-five year old Suchita Saini is a power press operator who has studied till grade VII. She moved to Faridabad 17 years ago from Bihar’s Chhapra with her four daughters and husband, a helper in a factory. In a power press accident in 2022, she lost three fingers. It was on a machine that had not been properly maintained.
Saini has resisted every effort by the factory owner, who she says routinely humiliates women, to remove her from the rolls. Their family is primarily supported by Saini’s monthly income of Rs 10,500.
After the accident, she was taken to a private dispensary “with two cots”, instead of the ESI hospital. “The factory was asking me to get my husband's ESI card,” she says. “Why would I get his card when I am the [power] press operator at the factory? I demanded that I be taken to the ESI hospital to be treated.” There is no maintenance at all, and there have been more accidents, she said.
Suchita Saini’s factory owner wants her removed from work. But she has resisted. She says that at her age and after the accidents, no one will employ her.
While an employer ought to generate an accident report which is to be submitted to ESI, it often does not happen, due to which treatment at a hospital is delayed. The accident report, which is supposed to be filed 24 hours after the incident being brought to the notice of the employer, informs ESI about the date and details of the accidents and where it happened. It helps calculate temporary and permanent disability benefits which are 90% of the wages. The permanent disability entitlement is finalised and certified by ESI medical board depending upon the extent of loss of earning capacity.
“The accident report generated by the employer ideally has the location of the accident, which means the state Industrial Safety and Health division under the labour department should be aware of the accidents,” said Saroja. “While the ESI data may reflect treatment, DGFASLI which also falls under the labour ministry may not have the same data.”
While Saini has received Rs 24,000 for medical needs through ESI, her salary, which was Rs 11,000 before the accident, was reduced to Rs 10,500. “We do not get a salary slip, but know that ESI contributions get cut because I get messages.”
Her friend, Savita Devi, a 36-year-old press operator is livid that the auto component unit employers that she works for had not made her ESI card at the time of her accident in which she lost her left index finger. When they finally made it, they got the details wrong.
Without the correct details, she cannot access disability entitlement and pension including Rs 3,000 a month from the Haryana government’s state disability pension.
Savita Devi’s ESIC card was made after an accident in which she lost her index finger.
“I am having to fight for my rights,” said Savita, a migrant worker from Bihar’s Sheikhpura. “I want to see how they [owners] will throw me out without giving my entitlements. Chorenge nahi, apna haq ke liye ladte rahenge [I won't give up without fighting for my rights.]”
Basanti has lost hope of help from her employer for surgery to replant her arms, and is struggling to find the strength to fight them. “I asked him to transfer a lump sum, which he did. But neither the contractor nor the owner bother anymore about my surgery. I have no hope from them.”
Some recommendations suggested by experts/SII to improve safety in auto sector supply chain
|
Kabir Dube, an intern at IndiaSpend, contributed to this story.
We welcome feedback. Please write to respond@indiaspend.org. We reserve the right to edit responses for language and grammar.