Explained: The Critical Mineral Foundation Missing In India’s Climate Ambitions
India relies on imports for most critical minerals needed for an energy transition--in an ever-volatile international market, spending precious foreign exchange
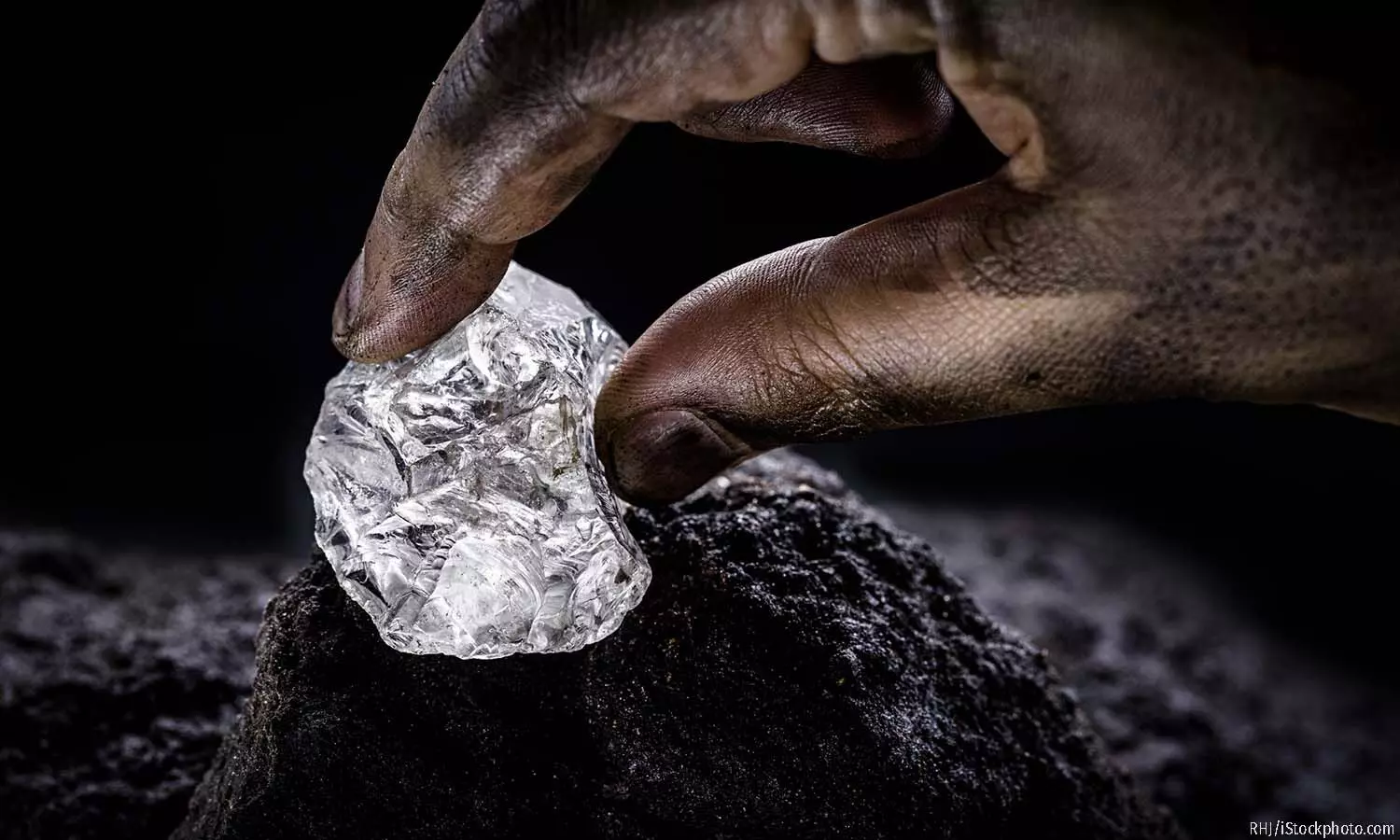
Mumbai: The Indian government has set ambitious climate goals, and industry, public sector undertakings and private players are following suit. But if we scratch beneath the surface, are the stepping stones in place?
What critical minerals does India need to fulfil these ambitions? How much of those do we have and how much do we import? The answers are not encouraging. On one hand, India is setting major decarbonisation targets but on the other, it relies heavily on the import of most critical minerals required for its climate ambitions, spending precious foreign exchange and dealing with an ever-volatile international market.
In 2023, the Indian government, for the first time, identified 30 critical minerals and is working towards securing them.
“Though India has not been a dominant player in the global supply chain for various critical minerals like lithium, cobalt etc., India has been working to strengthen its position in the mining and processing of critical minerals,” the Union Ministry of Mines had said last year.
India has resources of certain minerals but does not have processing capabilities while in others, India has no known reserves of minerals and is entirely dependent on imports (see table).
As India moves towards fulfilling its climate commitments, demand for these minerals is only going to increase, and supply will have to keep up or alternatives will have to be found.
Where does the world stand
The critical minerals required for energy transition fall into four major categories based on how they are used:
—Batteries: Cobalt, graphite, lithium, and nickel, for instance, are used in batteries such as those that power electric vehicles (EVs), and for grid-level storage.
—Permanent magnets: Many rare earth elements are used in permanent magnets, which are key components of, for example, EV motors and wind turbines.
—Electrification and infrastructure: Copper and aluminium are used in electrical wiring, transmission lines and transformers, for example.
—Other applications: Other critical minerals include iridium, used in electrolysers that enable the production of hydrogen, and silicon, for the manufacture of solar panels.
As on date, deployment of low-emission technologies is only at about 10% of the levels required by 2050 in most areas, and even that has been in comparatively easy use cases.
Many of the critical minerals required for energy transition, including cobalt, lithium, natural graphite, nickel and rare earth elements, rely on the three largest supplying economies for more than 50% of their extraction, and more than 80% in the most extreme cases, according to an August 2024 review by McKinsey Global Institute.
For instance, Australia, Chile and China account for about 90% of the global supply of lithium. The Democratic Republic of Congo accounts for more than 75% of cobalt extraction, and China for more than 60% and 80% respectively of the extraction of rare earth elements and natural graphite, the review noted.
China accounts for more than 60% of the refining of cobalt, lithium, natural graphite, and rare earth elements.
Further, China currently dominates all stages of the solar photovoltaic value chain, according to a June 2024 working paper from the Centre for Social and Economic Progress (CSEP). The country produces 79% of global polysilicon, 97% of wafers, 85% of cells, and 75% of modules. This is concentrated in just a handful of Chinese companies. India does not participate in the upstream stages of solar manufacturing, and has a 1% share in cell production and a 3% share in module production, the paper noted.
While India expects to meet its short-term solar capacity demand through imports of modules and panels, the longer-term requirements are expected to be high and the supplies are considered risky.
China accounts for 69% of global neodymium extraction and 85% of neodymium processing. Neodymium is used in the production of permanent magnets, as mentioned above.
Further, China produces 75% of all Li-ion batteries, along with 70% of cathodes and 85% of anodes. Indian companies have begun some value addition in battery chains and supply chains, but their global share is negligible, and almost all demand for battery components is met through imports, the working paper noted.
Demand-supply gap
Taking all uses into consideration, in five years to 2022, global demand for lithium increased threefold, doubled for neodymium, and rose 70% for cobalt and 40% for nickel from 2017 to 2022. The market size of the critical minerals doubled to $320 billion.
Under McKinsey’s 2023 Achieved Commitments scenario, demand for seven of the eight critical minerals investigated--lithium, cobalt, nickel, dysprosium, terbium, neodymium, and praseodymium--could escalate inordinately by 2030. For example, demand for nickel could double, demand for dysprosium and terbium could quadruple, and demand for lithium could increase sevenfold.
And the next few years are likely to see a ‘particularly pronounced’ increase in demand, as that is when most new low-emissions technologies will likely experience the fastest growth in deployment. After 2030, the review estimates that demand will continue to grow, but at a slower pace.
Supply, however, is not projected to grow as fast as demand under the transition, potentially leading to imbalances.
The physical challenge of expanding the supply of critical minerals is not that there are insufficient critical minerals in the ground, but rather that it takes time for new extraction projects to come online.
“In fact, resources and reserves of metals and materials such as copper, lithium, and nickel have been increasing as more exploration has been undertaken and, indeed, are at an all-time high,” the McKinsey Global Institute review says. “However, lead times to access these reserves can be very long and outcomes uncertain.”
The review cites an estimate from the IEA which shows that, on average, it has taken 17 years for critical minerals projects to go from discovery to production over the past decade. Copper and nickel projects have the longest lead times at 13 to 19 years, while lithium projects become operational quicker, at about five years.
This variation in lead times is a function of a number of factors. The complexity of accessing the ore can play a large role. Scaling up the infrastructure such as access to power, water roads, railway lines and ports is also time-consuming, especially the mines are in remote locations.
Because, as pointed out earlier, extraction and the refining of critical minerals is highly concentrated in a few countries around the globe, sufficient access to refined minerals relies on the stability of global trade flows. Another significant constraint is a shortage of skills, especially in refining.
How can the supply be accelerated? Streamlining the permissions and planning processes can help, the review says, adding that recent developments in new extraction technologies, surveying approaches, and modular construction could accelerate lead times.
Even then, the demand for critical minerals would need to be managed by increasing efficiency of use, substitution, and the use of new technologies such as sodium-ion batteries and rare-earth-free motors.
While some of these solutions are beginning to be deployed, the process is still at a “relatively early” stage, the review says, and there could be as yet unquantified performance trade-offs.
Miles to go for India
A committee appointed by the Ministry of Mines had, as we said, for the first time identified 30 minerals critical to India’s development, based on a detailed assessment and a criticality index. It submitted its report in 2023.
“Critical minerals such as lithium, copper, cobalt, graphite and [others] …. are essential for their uses in green technologies like solar panels, wind turbines, batteries, and electric vehicles which are integral to the transition toward clean energy and a low-carbon economy,” a press note issued by the ministry reads.
Reserves of critical minerals have been found in Andhra Pradesh, Arunachal Pradesh, Bihar, Chhattisgarh, Gujarat, Jharkhand, Karnataka, Madhya Pradesh, Maharashtra, Odisha, Rajasthan, Tamil Nadu, Uttar Pradesh and Jammu and Kashmir.
The CSEP working paper notes that while India does produce copper, silicon and silver, it relies more heavily on imports for copper and silver. Further, given India’s ambitions for domestic solar manufacturing--and the fact that there are no known resources for other critical minerals needed for solar photovoltaic manufacturing--companies need to find foreign sources for these minerals. The paper points out that indium, gallium and germanium have high supply risks “due to their concentrated extraction and processing in China”.
India also has large untapped resources of minerals like cobalt, lithium, and rare earth elements. Many critical minerals are deep-seated, the paper explains, thus requiring high-risk investments in exploration and mining.
Ganesh Sivamani, associate fellow at CSEP who co-wrote the paper that was referred to by the Union Ministry of Mines while making the list, said, “Demand for critical minerals is going to increase. The government is trying to encourage demand but the problem is, in some cases, we don’t have the capacity to actually convert a mineral into the form that's required for the technology.
“As a geopolitical issue, do we want to rely on Chinese technology imports?,” Sivamani asks. “I don't think that's something the current political climate will allow for.”
With considerations like these in mind, the Ministry of Mines has entered into bilateral agreements with resource-rich countries such as Australia, Argentina, Chile, Mozambique etc. which have rich critical mineral resources and access to the latest technologies in their exploration and development.
The joint venture company Khanij Bidesh India Ltd. (KABIL), which comes under the ministry, has acquired 15,700 hectares in the Catamarca province of Argentina for exploration and mining of lithium.
Vivek Bharadwaj, Secretary, Ministry of Mines had stated that international commitments towards reducing carbon emissions requires the country to urgently relook at its mineral requirements for energy transition and net-zero commitments. “The Ministry will be revisiting the critical mineral list periodically,” he added.
Further, connecting new clean energy sources to the grid will need upgrades to existing transmission infrastructure, which in turn will need critical minerals such as copper, zinc, tin and silver.
Experts suggest a multi-pronged strategy to achieve self-sufficiency. There are certain minerals for which there are no known resources in India. Researchers believe that policymakers need to promote reconnaissance in greenfield areas (regions where mining activities have not yet taken place) with high geological potential. Further, manufacturers of green technology equipment “would need to look at foreign sources” to secure their mineral requirements in ores, processed ores etc.
In cases where India produces a mineral, the CSEP paper says, strategies should focus on bolstering the domestic mining and processing regimes. India can share its expertise and invest in countries seeking to expand their own domestic capabilities.
For minerals that India does have reserves of, but a relatively high share of demand is being met through imports due to low self-sufficiency, “efforts may be made to allocate more mining blocks to boost production levels”, the paper says.
For minerals where there are known resources in India but no economically mineable reserves, policymakers can encourage the private sector to take up exploration activities.
However, building domestic capacity will not be easy.
“This is something that China has been doing for multiple decades, which has given them a lot of advantage in both cost and scale,” Sivamani points out. “So, if India is to catch up on the technologies of today, it's going to take a lot of investment, a lot of expertise.”
(Kanishk Shetty, intern with IndiaSpend, contributed to this report)
We welcome feedback. Please write to respond@indiaspend.org. We reserve the right to edit responses for language and grammar.